FAILURE ANALYSIS ON PLASTICS AND METALS
We perform failure analysis on plastics and metals to determine the causes which have brought products and machinery to sudden failure.
Wish you find a remedy after a material rupture?
When a failure analysis is performed?
Failure analysis is performed when a system, equipment or component is subjected to an early, sudden or unexpected failure.
The key principles of this analysis are applicable to any branch of the manufacturing sector since the triggering factors can be divided into three specific classes:
- Chemistry and microstructure of the material;
- Manufacturing process parameters and operating conditions;
- Influence of external factors such as an aggressive environment, thermal or mechanical load conditions.
Our working method during failure analysis
Inspection on-site
Failure analysis begins with a series of field surveys, where video inspections and microscopic analysis can be performed with the purpose of determining the type of fracture, its initiation and the level of environmental harshness.
Field surveys allow the identification of areas of greatest interest, from which samples can be taken for subsequent laboratory investigations such as optical or electron microscopy, spectroscopy, and X-ray diffraction.
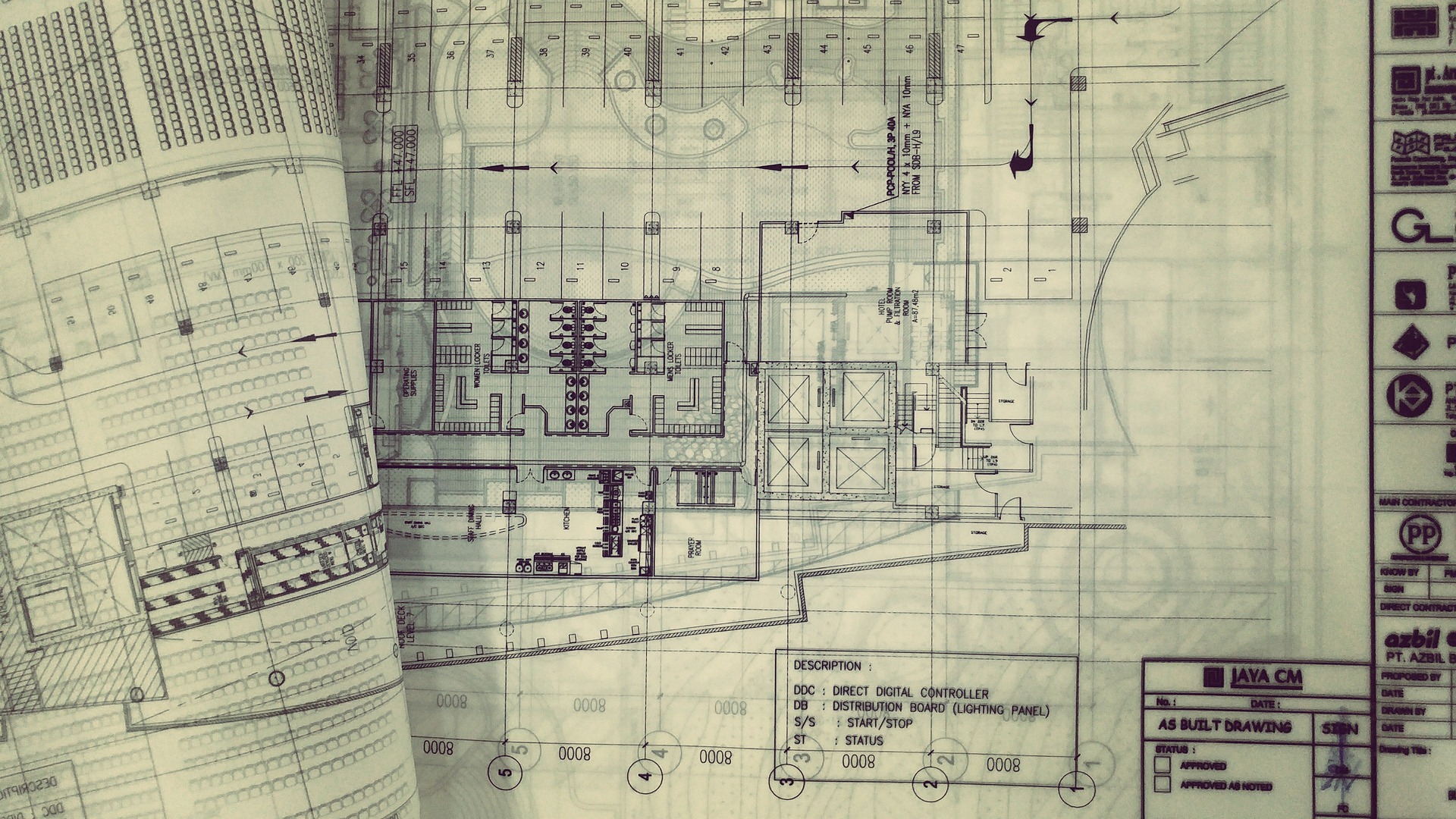
Internal analysis and the customer role
At this stage, we collect information on the number of failures encountered, batch traceability, and any changes introduced in the production cycle (suppliers, process parameters, etc.).
Collaboration with the customer is of paramount importance since this information cannot be obtained from the analysis of materials, although it affects their performance and strength.
Which materials can a failure analysis be performed on?
Only after being drawn an overall picture, targeted laboratory analyses are conducted. The great expertise gained in technical support to customers allows us to offer professional services in the following areas: components made of steel and other metal alloys, failure analysis on plastics (e.g. extruded or moulded parts), composite materials with thermoplastic and thermosetting matrix, paints, varnishes and coatings and adhesives.
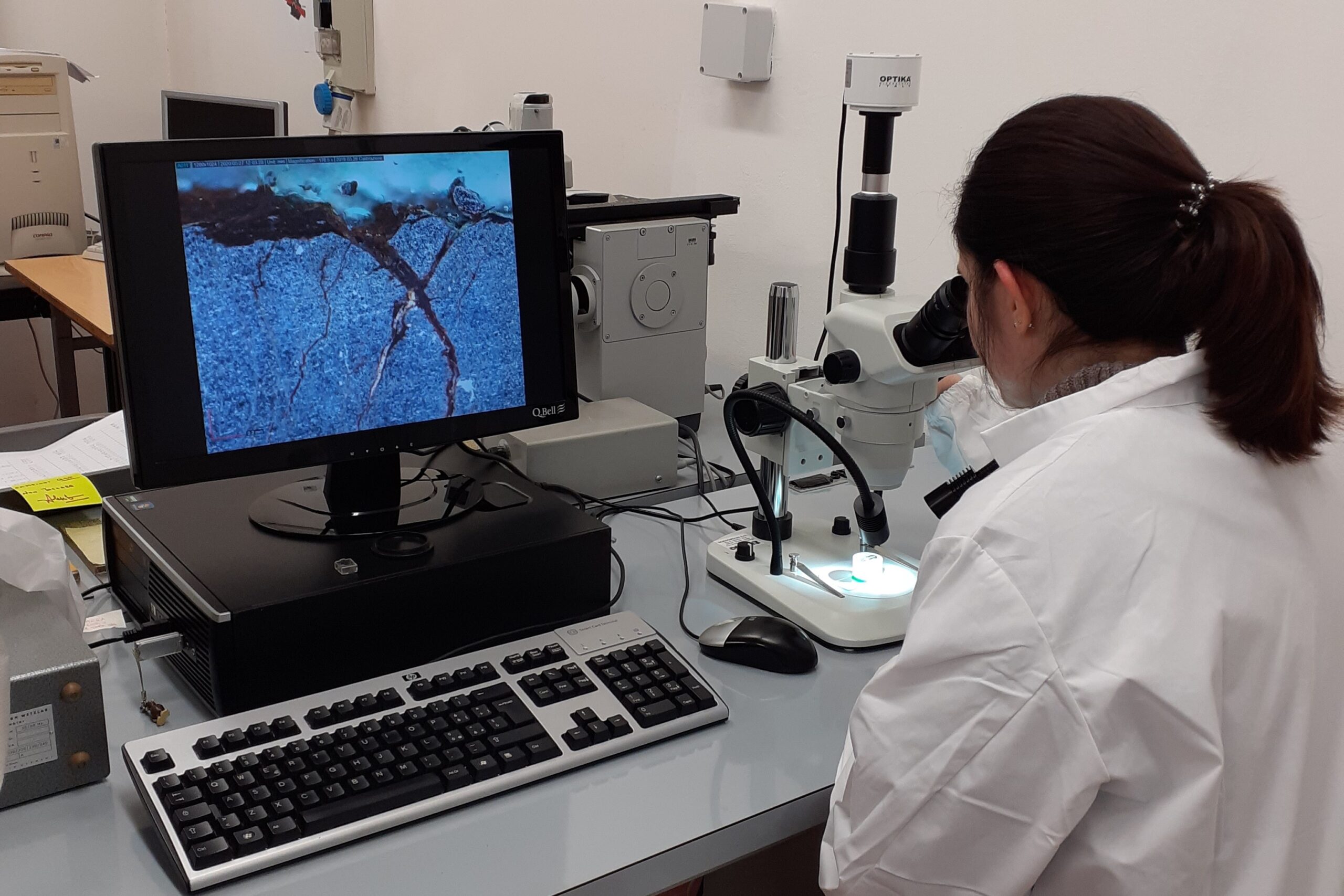
FAILURE ANALYSIS ON PLASTICS
The main properties we investigate with infrared spectroscopy during a failure analysis on plastic products refer to the type of polymer (thermoplastics, thermosetting and elastomers) and the changes introduced by thermal, chemical, and environmental degradation mechanisms.
Afterwards, using differential scanning calorimetry (DSC), our laboratory can determine the structure, the behaviour during melting and crystallization, glass transition temperature, decomposition temperature, crystallinity degree, additives and phases (fillers, blends, copolymers).
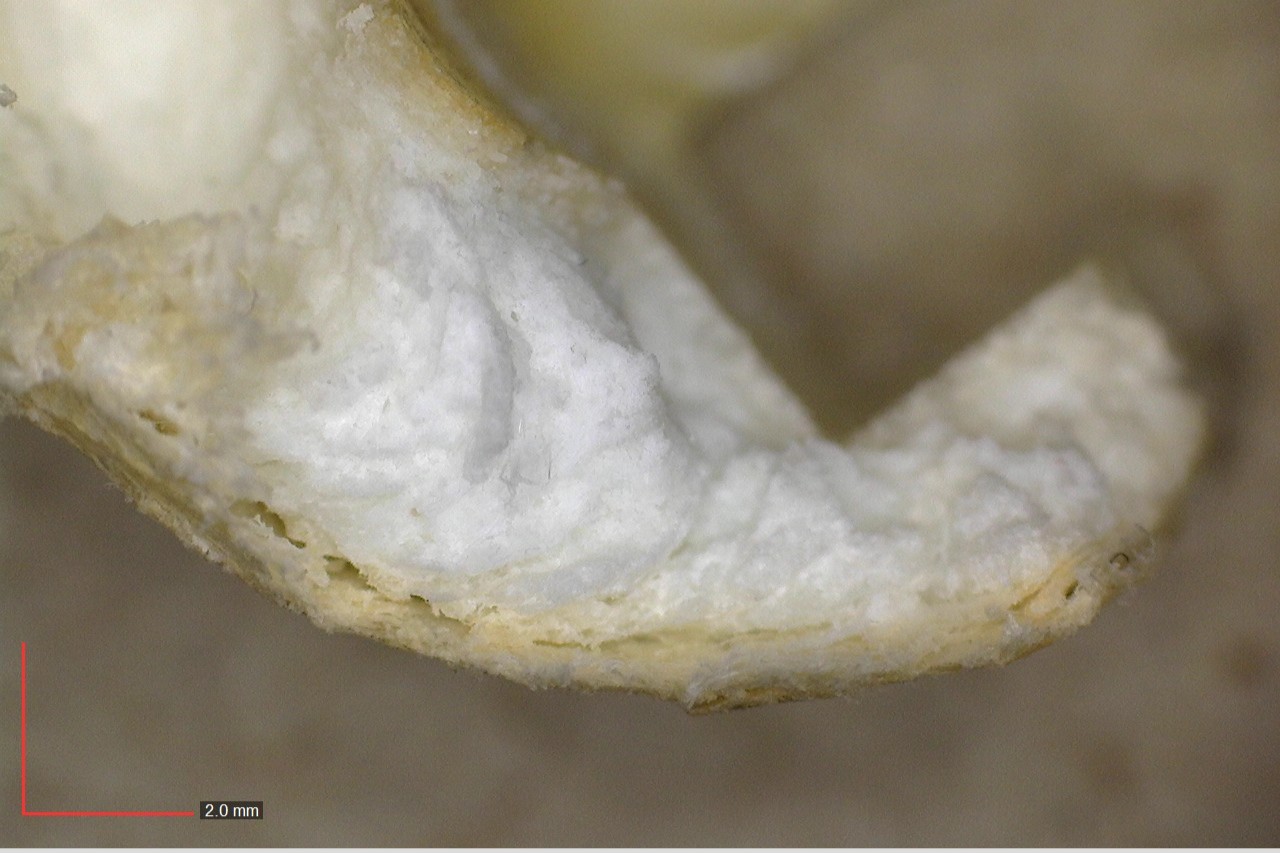
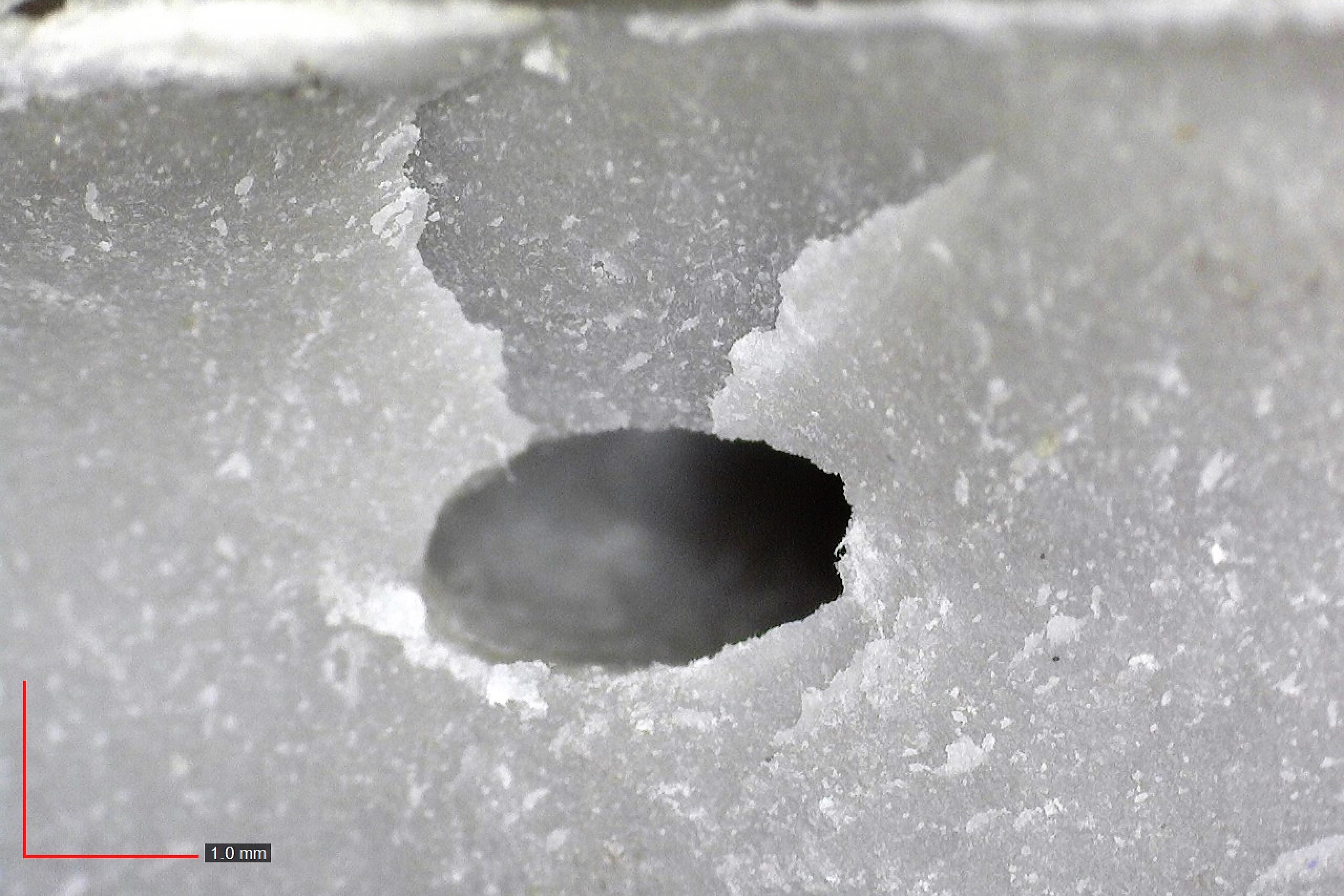
FAILURE ANALYSIS ON METALS
The mechanical properties of metals, such as steel, cast iron and non-ferrous alloys (aluminium, copper, nickel, etc.) are strongly influenced by their chemical composition and microstructure. After accurate preparation and polishing, samples are carefully evaluated focussing particular attention on the effects of heat treatments and processing on:
- phase distribution
- grain dimension
- steel microstructure (austenite, ferrite, pearlite, martensite, sorbite, bainite)
- inhomogeneities and non-metallic inclusions.
Visual examinations both macroscopic (with optical microscope) and microscopic (by means of metallographic microscope with a magnification greater than 50x) are performed in order to evaluate fracture propagation.
We can employ scanning electron microscopy (SEM) combined with EDS microanalysis if a more detailed evaluation is required to characterize, for example, fracture morphology (mechanical or stress corrosion cracks, dimples) and oxidized or corroded surfaces.
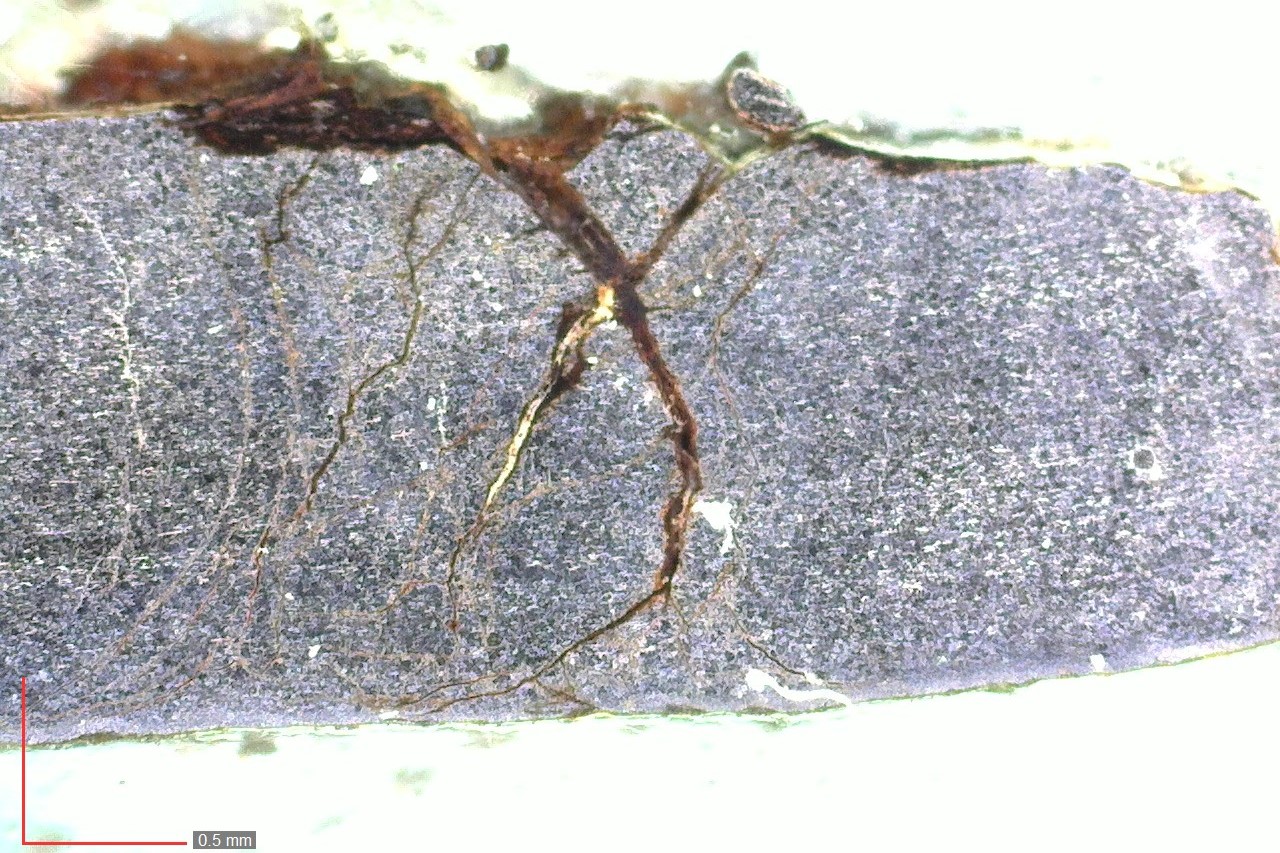
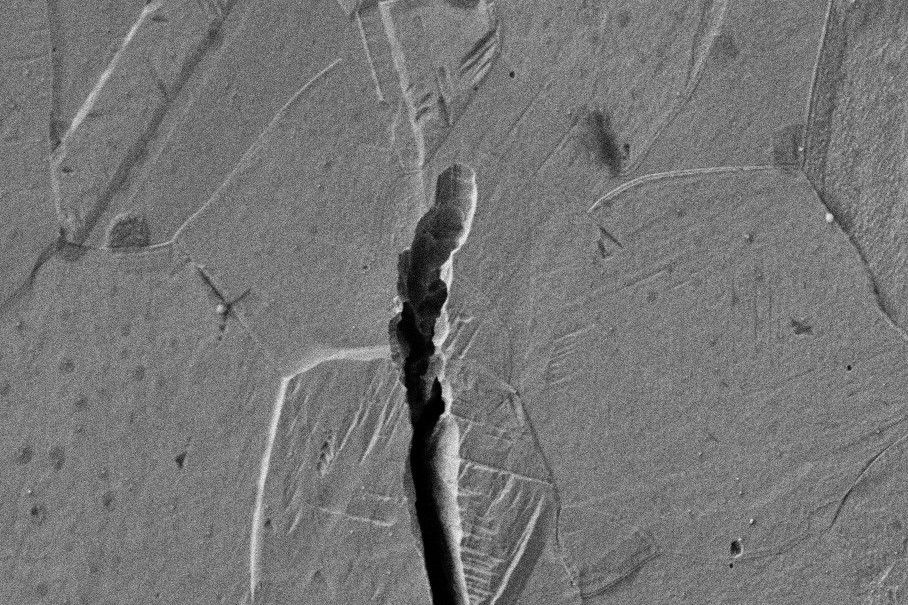