This article, the result of collaboration between Cotec Labs and MaterialScan, focuses on the importance of protective coatings for fasteners, particularly in sectors like the automotive industry, and on the effectiveness of corrosion tests in evaluating their resistance and durability.
The problem of corrosion
Corrosion represents a significant challenge as it causes considerable economic losses (3-4% of global GDP). Corrosion can compromise the performance and lifespan of any product, including fasteners, with potential safety implications.
“Corrosion can damage any product, reducing its lifespan and compromising its performance, resulting in safety issues and economic losses.“
Corrosion tests: evaluation and improvement
Manufacturers employ various corrosion tests to evaluate and enhance the resistance of their products. These include:
- salt spray tests
- humidity tests
- immersion tests
- cyclic tests.

These tests, often required by automotive OEMs, simulate the aggressive environmental conditions that products might encounter during their use.
“Although accelerated tests offer a simplified view of real conditions, they help manufacturers evaluate the coating’s ability to prevent corrosion and decide whether a further protective layer is needed.“
Surface treatments: a crucial factor
The choice of surface treatment is crucial to ensure the quality, durability, and functionality of fasteners. Different treatments offer specific characteristics and resistance to damage, scratches, and chemical agents.
The article focuses on three types of coatings:
- alkaline zinc: economical with uniform consumption, suitable for moderately corrosive environments;
- zinc-nickel: resistant to high temperatures, hard and durable, ideal for extremely corrosive environments;
- zinc flakes: excellent anti-corrosive properties, high chemical resistance and low electrical conductivity, perfect for applications in marine environments.
Cyclic Corrosion Tests: a more realistic approach
Cyclic Corrosion Tests (CCT) are a more realistic alternative to neutral salt spray tests (NSS) to evaluate the durability of fasteners under variable atmospheric conditions.
“This opens the door to cyclic corrosion tests.“
Cyclic corrosion testing tailored and approved by the specific OEM is what normally is required. These test methods are often developed with decades of studies of corrosion processes, in a lab environment and cyclic chamber compared to real environment.
The following figure illustrates the phases constituting the corrosion cycle (ACT1) developed by Volvo. For most of the week, sub-cycle 1 is repeated twice a day, except on Monday and Friday when sub-cycle 2 is used for the second part of the day (12 hours). As can be noted, only sub-cycle 2 includes three phases where salt fog is on for 15 minutes each.
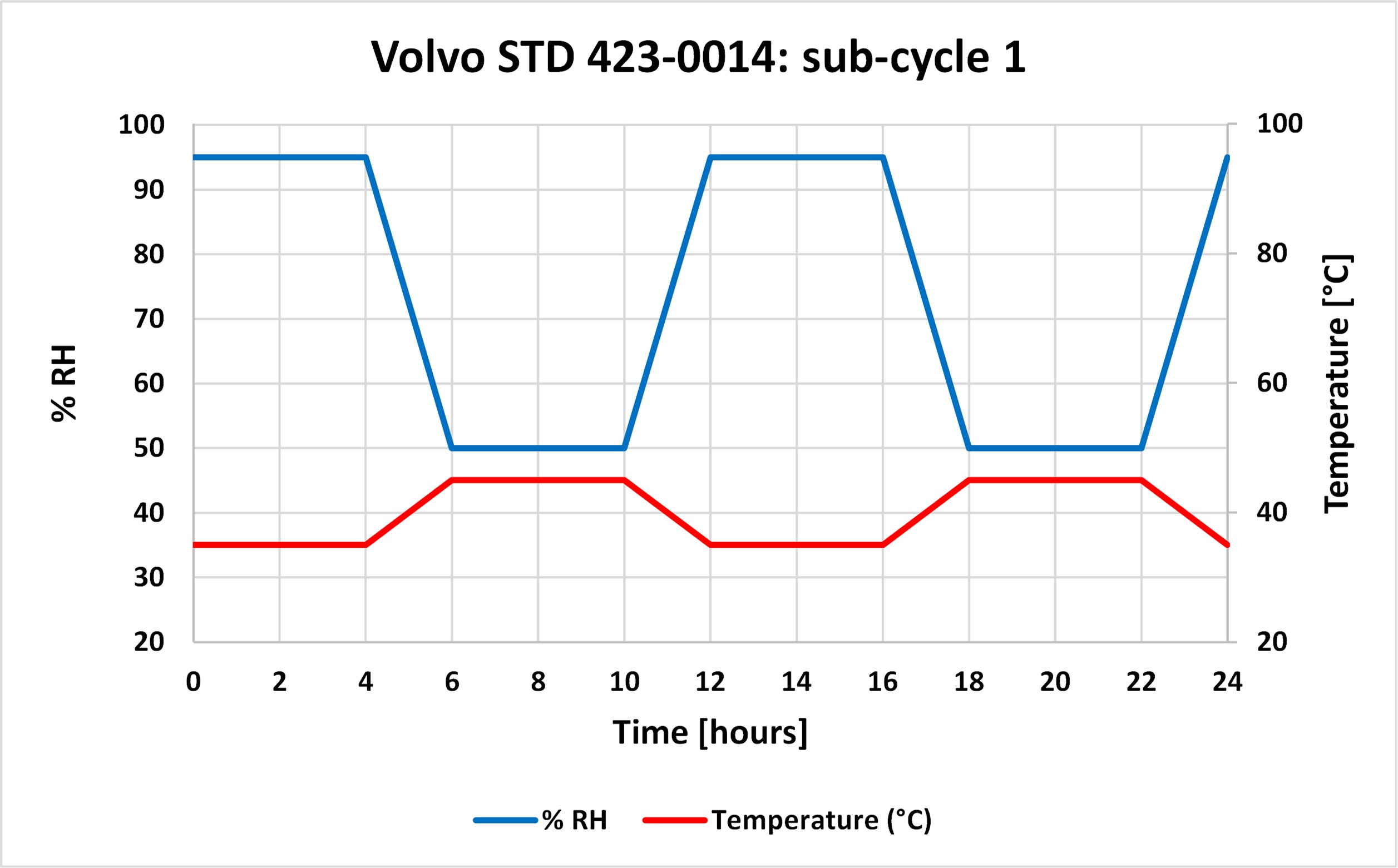
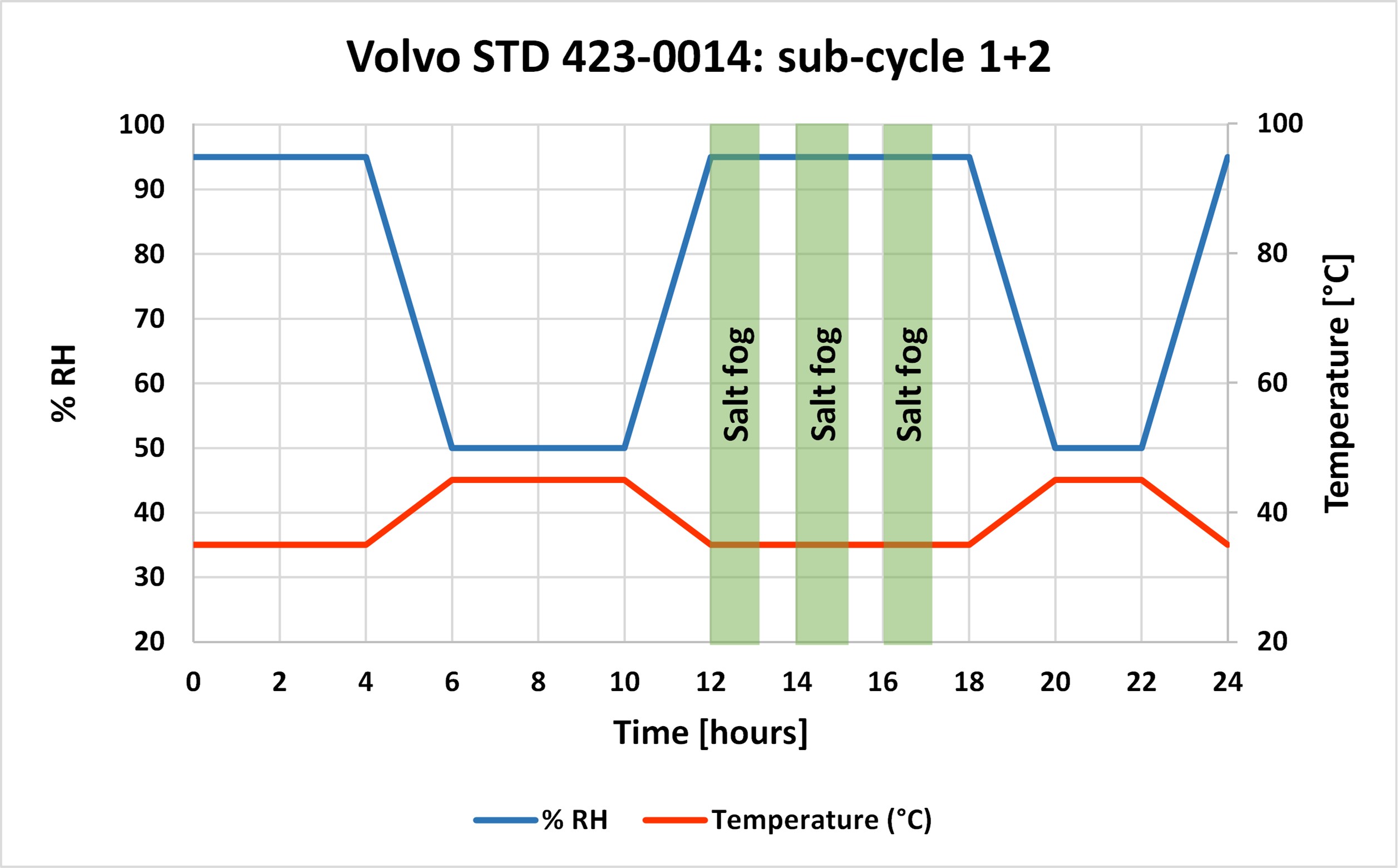
Conclusions
The article emphasizes the importance of selecting the most appropriate coating and corrosion test method for the specific application. Cyclic corrosion tests offer a more accurate simulation of real-world conditions, ensuring the quality and durability of fasteners, particularly in aggressive environments such as those faced in the automotive industry.
The collaboration between Cotec Labs and MaterialScan stands as a benchmark for the Italian industry, offering a high-quality analysis and testing service for coating evaluation and compliance with OEM requirements.