Come scegliere un test di corrosione per la qualifica di un prodotto?
Il Rapporto Tecnico ISO/TR 16335 fornisce alcuni ottimi suggerimenti per la scelta del test di corrosione più adatto a qualificare prodotti realizzati in materiale metallico provvisti o meno di un rivestimento protettivo.
La Tabella 1 riassume i principali metodi di prova utilizzati. Il metodo di laboratorio più diffuso è il test in nebbia salina neutra costante (categoria A). Questo tipo di test è utile a rilevare discontinuità come pori e altri difetti in alcuni rivestimenti metallici, strati di conversione (es. ossidazione anodica) e rivestimenti organici. Tuttavia, sebbene questo sia ampiamente utilizzato per le prove di qualifica, i risultati delle prove in nebbia salina costante raramente sono correlabili con il comportamento dei componenti in servizio.
Un modo per migliorare tale correlazione consiste nel combinare l’esposizione alla nebbia salina con cicli di umidità facendola variare tra una condizione di condensa e una a basso livello di umidità (categoria C) introducendo così anche una fase di asciugatura nel ciclo di prova di corrosione.
Alcuni inquinanti atmosferici, come l’anidride solforosa SO2, il diossido di azoto NO2, l’acido solfidrico H2S e il cloro Cl2, presenti nell’aria in tracce favoriscono la corrosione dei metalli in condizioni di umidità elevata. I test di esposizione ad alta umidità in presenza di tali inquinanti atmosferici sono quindi spesso utilizzati nella qualifica dei prodotti elettronici (categoria D).
Per valutare la resistenza alla corrosione di alcuni prodotti, sono stati introdotti anche test che combinano la nebbia salina intermittente con l’esposizione a gas che favoriscono la corrosione (categoria E).
Tabella 1 – Categorie di prove di corrosione atmosferica accelerata.
Categoria di prova | Esempi di normative | |
A | Nebbia salina costante | ISO 9227, IEC 60068-2-11 |
B | Immersione alternata degli oggetti di prova in una soluzione salina seguita da asciugatura o nebbia salina intermittente e asciugatura | ISO 11130 |
C | Prove con variazione ciclica dell’umidità (asciutto/bagnato), comprensive di fasi in nebbia salina | ISO 11474, ISO 14993, ISO 11997-1, ISO 11997-2, ISO 16151, ISO 16701, ISO 20340, IEC 60068-2-52 |
D | Prove con esposizione continua ad atmosfere con basse concentrazioni di gas che favoriscono la corrosione e ad umidità moderatamente elevata | ISO 10062, IEC 60068-2-60 |
E | Prove con esposizione continua ad atmosfere con concentrazioni più elevate di gas che favoriscono la corrosione e con un’umidità più elevata, comprensive anche di fasi di asciugatura e un breve periodo di spruzzatura di sale | ISO 21207 |
F | Test con umidità elevata | IEC 60068-2-78, IEC 60068-2-30, NT ELEC 025 (con condensa) |
Anche le prove che prevedono l’esposizione dei provini a un’elevata umidità e all’acqua di condensa sono considerate prove di corrosione (categoria F). Tali prove possono produrre effetti di corrosione sulle parti metalliche se sono presenti contaminanti superficiali sotto forma di sali. Questi test sono utilizzati anche per testare i rivestimenti organici perché possono indurre danni causati dal rigonfiamento e dalla fuoriuscita di additivi. Per i test sui dispositivi elettronici si utilizzano test ad elevata umidità per verificare l’ermeticità e le infiltrazioni d’acqua nelle apparecchiature. Un metodo di prova particolare prevede di testare la capacità di protezione dalla corrosione di un involucro semipermeabile di un dispositivo elettrico, sottoponendo l’involucro ad un rapido raffreddamento. Se l’effetto del raffreddamento è sufficientemente elevato questo provoca l’immissione di aria umida all’interno dell’involucro e la conseguente condensa del vapore acqueo.
Prove di corrosione in funzione del campo di applicazione
La Tabella 2 riporta quattro campi di applicazione caratterizzati da tre diverse corrosività dell’ambiente in cui un determinato componente si trova ad operare. Per ciascuna combinazione la tabella suggerisce quale sia la categoria di prova di corrosione più idonea per la qualifica dei prodotti (P = preferita, U utile per comparare prodotti simili, N = utile solo per controllo qualità su prodotti uguali).
Tabella 2 – Categoria di prova di corrosione e campi di applicazione.
Campo di applicazione | Idoneità delle categorie di test di corrosione | ||||||
Descrizione | Corrosività |
A nebbia salina costante |
B immersione alternata |
C cicli umidità + nebbia salina |
D esposizione a gas inquinanti |
E esposizione a gas inquinanti + nebbia salina ed asciugatura |
F condensa |
Costruzioni marittime |
Parte superiore (C4-C5) |
N | U | P | – | P | – |
Zona degli spruzzi (C5) |
N | U | – | – | – | – | |
Immersione | – | – | – | – | – | – | |
Automotive |
Scocca (C4-C5) |
N | U | P | – | P | – |
Vano motore (C2-C4) | N | U | P | – | P | – | |
Abitacolo (C1) | – | – | – | P | – | P | |
Costruzioni edili |
All’aperto (C3-C5) |
N | U | P | – | P | – |
Zona riparata (C2-C4) |
N | U | P | – | P | – | |
All’interno (C1-C2) |
– | – | – | P | – | P | |
Dispositivi elettrici |
Severa (GX) |
U |
U |
U |
– | P | P |
Elevata (G3) |
U |
U |
U |
– | P | P | |
Da lieve a moderata (G1-G2) |
– | – | – | P | – | P |
Confronto tra alcune metodologie di prova
Per molte metodologie di prova sono disponibili, all’interno delle norme stesse, dati sull’entità della corrosione di campioni metallici standard sottoposti a tali test. Per illustrare come varia il processo corrosivo tra alcuni test standardizzati, nella Tabella 3 sono riportati i tempi medi di prova stimati per raggiungere una perdita di massa dell’acciaio al carbonio pari a 670 g/m², corrispondente a circa 5 anni di esposizione atmosferica nella categoria di corrosività media C3, così come definita dalla norma ISO 9224.
Tabella 3 – Confronto del tempo medio necessario per raggiungere una perdita in peso di acciaio al carbonio pari a 670 g/m² a seconda del metodo di prova.
Metodo di prova | Giorni per raggiungere una perdita in peso di acciaio al carbonio pari a 670 g/m² a causa della corrosione |
Esterno C3 (conforme ISO 9224) | 1780 |
Esterno C4 (conforme ISO 9224) | 622 |
Esterno C5 (conforme ISO 9224) | 143 |
Esterno CX (conforme ISO 9224) | 15 |
ISO 9227 | 19 |
ISO 14993 | 7 |
ISO 16701 | 19 |
ISO 11997-1 | 32 |
Test ciclico vs. nebbia salina
Le figure seguenti mettono a confronto due piastrine standard rivestite con il medesimo processo di verniciatura sottoposte per 1008 ore a due tipi di prove diverse: a sinistra quella sottoposta ad un test di corrosione ciclico, a destra quella in nebbia salina neutra costante.
L’estensione della corrosione a partire dall’intaglio è chiaramente visibile su entrambi i campioni rivestiti ma molto più severa nel caso della corrosione ciclica.
Analoghe considerazioni possono venir fatte anche per l’immagine di copertina dove vengono illustrate due staffe identiche.

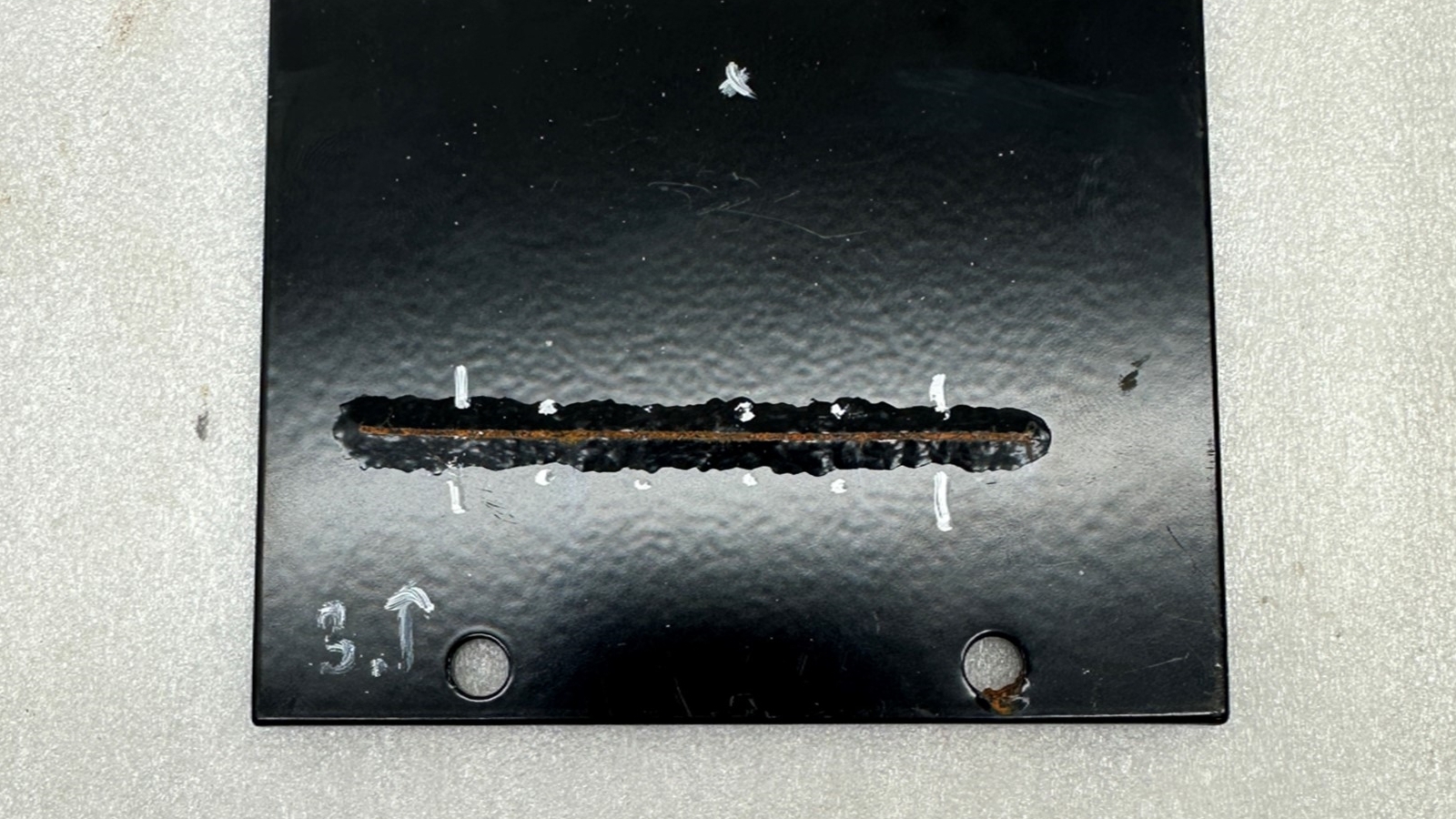
È sempre bene ricordare che non è possibile utilizzare i risultati delle prove di corrosione per predire il comportamento a lungo termine del rivestimento, poiché le condizioni ambientali incontrate nella pratica sono molto più complesse e perciò difficili da simulare.
I dati qui riportati devono essere intesi come espressione del know-how industriale accumulato nel corso degli anni.
Hai bisogno di un supporto specialistico?
In MaterialScan comprendiamo l’importanza di garantire che i tuoi prodotti siano all’altezza degli standard più elevati. Il nostro servizio di test di corrosione unico in Italia e senza costo aggiuntivo supporta i clienti nella selezione del metodo di prova più corretto in base ai specifici requisiti di prodotto.
Consulta il catalogo test, chiamaci al numero: +39 351 723 9441 oppure scrivi a: material@materialscan.it.